Compressed air system
Compressed air system solution
A compressed air system is an essential part of many modern production environments, from powering pneumatic tools in manufacturing to delivering sterile pressurized air in pharmaceutical settings. The systems are populair because they are clean, flexible and safe compared to other energy sources. However, compressed air systems are also known for being energy-intensive. That’s why it’s vital to choose the right air compressor system, built with reliable components such as rotary screw air compressors, air dryers, and air receiver tanks. Even a small optimization can lead to substantial energy cost savings and increased operational efficiency.
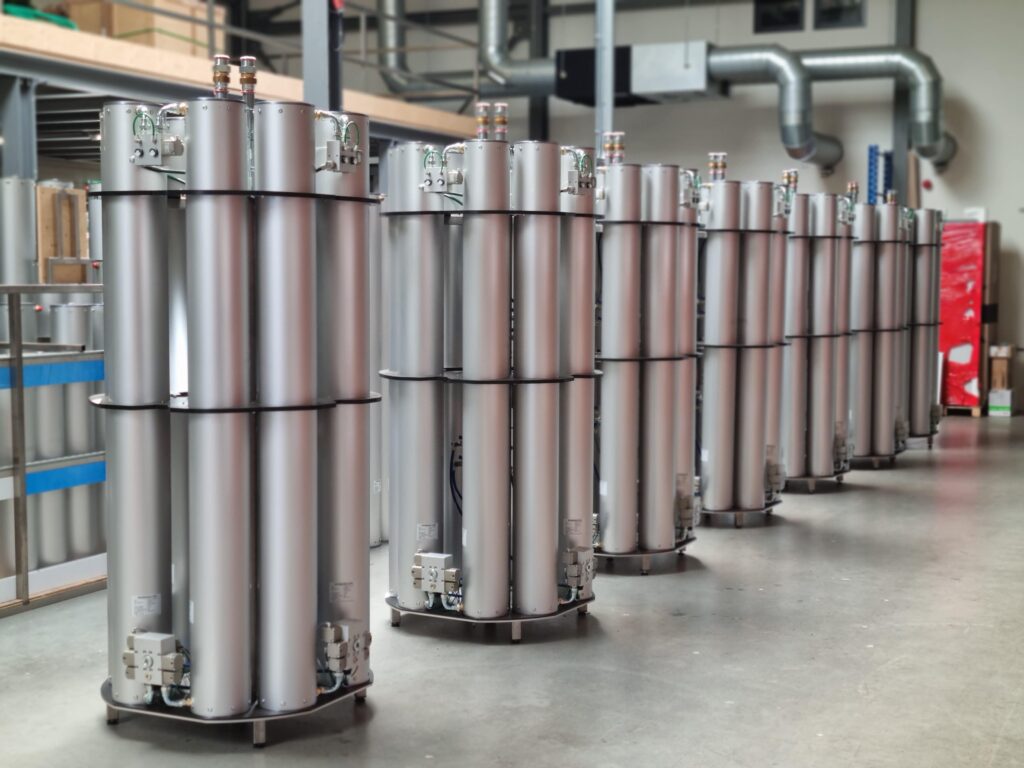
What is a compressed air system?
A compressed air system consists of components that compress, treat, store, and distribute pressurized air for industrial applications. A motor-driven air compressor draws in atmospheric air, compresses it to raise pressure, and sends it through air treatment components like air dryers and air filters to remove excess moisture, oil, and dust. The clean, dry air is stored in an air receiver tank (or storage tank) before being distributed via a piping network to various air tools, machines, or automated valves. Our compressed air systems include sensors, controllers, and feedback loops to maintain system pressure, reduce pressure drops, and prevent air leaks. Presscon’s PEC Controller plays a central role in optimizing these elements for energy-efficient operation.
When do you need a compressed air system?
Compressed air is a versatile and safe alternative to electrical power, especially in industrial settings. It’s often referred to as the fourth utility, after electricity, water, and natural gas.
Manufacturing and automation:
Factories use compressed air to power pneumatic tools (like impact wrenches, drills, paint sprayers), operate cylinders and robotic actuators, run conveyor belts, and perform material handling. Air-driven tools are often lighter and safer than electric versions since compressed air contains no spark risk and can run continuously without overheating.
Food, beverage, and pharmaceuticals:
Clean, dry compressed air is used for processing and packaging in these sectors. Examples include air jets for cutting or peeling produce, mixing or agitating liquids and powders, conveying food items, bottling drinks, and vacuum sealing packages. Because it can be made extremely clean (oil-free and filtered), compressed air is ideal for sensitive products. For instance, it provides sterile air for pharmaceutical production and maintains hygienic conditions in food processing lines.
Chemical and petrochemical industries:
Compressed air provides a safe energy source in flammable or hazardous environments. It powers control valves and instruments, aerates and mixes chemical mixtures, and drives pumps to transfer liquids.
HVAC and building systems:
Large commercial buildings use compressed air in HVAC control systems (e.g. pneumatic thermostats and valve actuators for heating/cooling systems). Compressed air also powers the brakes in elevators and amusement park rides, and is used in sprinkler systems or pumping for wastewater in facilities
Healthcare and breathing air:
Hospitals and clinics rely on highly purified compressed air for respirators and ventilators, surgical instruments, and dental tools.
Key compressed
air system components
Every compressed air system relies on a set of essential components that work together to produce clean, dry, and reliable pressurized air. Understanding these components is key to ensuring consistent performance, minimizing downtime, and improving energy efficiency in any industrial air compressor system.
These components form the foundation of a reliable and energy-efficient system. When properly configured, they ensure stable operation, reduce maintenance costs, and extend the lifespan of your equipment in even the most demanding industrial environments.
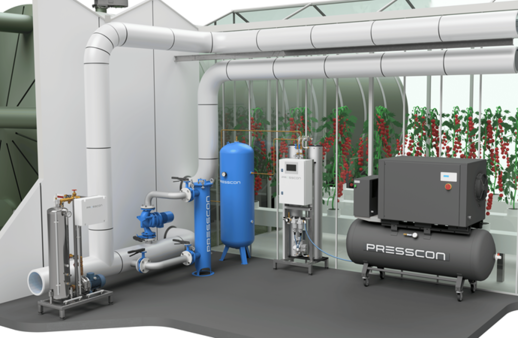
Air Compressor
The air compressor is the heart of the system. Most setups use rotary screw compressors or other positive displacement types to draw in ambient air and compress it to the required pressure. This compressed air is then delivered through piping to power pneumatic tools, machinery, and automated processes.
Compressed air tanks
Air receiver tanks act as a buffer between the compressor and the distribution system. They store pressurized air, reduce pressure fluctuations, and help accommodate sudden peaks in demand. Proper tank sizing ensures smoother operation and allows compressors to run more efficiently with fewer start/stop cycles.
Air dryer
An air dryer removes excess moisture from compressed air to achieve the required dew point (air dryness). Compressed air coming out of the compressor is hot and saturated with water vapor; as it cools, water condenses which can rust pipes and damage equipment. Refrigerated dryers chill the air to condense and remove water, usually getting dew point around 35-40°F (2-5°C). Desiccant dryers absorb water vapor to achieve even lower dew points (down to -40°F/C or drier) for sensitive applications. Removing moisture is critical because dry air prevents corrosion and microbiological growth in the system.
Air filters
Air filters are installed to remove oil particles, dust, and other contaminants from the discharged air. Clean air protects downstream equipment and ensures compliance with air quality standards, especially in sectors like food, pharma, and electronics. Multiple filter stages may be used depending on required purity levels.
Controls and instrumentation
For example, pressure switches or electronic controllers start/stop compressors or unload them to maintain target pressure; safety relief valves protect against overpressure in tanks; and our compressed air systems have central controllers to coordinate multiple compressors. Monitoring devices (pressure gauges, dew point monitors, flow meters) help in operating the system efficiently. All these components work together to ensure the compressed air is delivered at the right pressure, flow, and quality for the intended application.
Key parameters and sizing for a compressed air system
- Pressure (PSI / bar): The required system pressure depends on the specific applications and the equipment in use. Most industrial compressed air systems operate between 6 and 8 bar (87–116 PSI), although some processes require pressures outside this range. Operating at the lowest effective pressure can help reduce energy consumption; each reduction of 1 bar may result in energy savings of up to 7%.
Tip: Overpressurization often leads to unnecessary energy use. Pressure regulators and intelligent control systems such as the PEC Controller support maintaining a balanced pressure level.
- Flow rate (CFM / l/s): Flow rate is commonly expressed in CFM (Cubic Feet per Minute) or liters per second (l/s) and indicates the amount of air needed to operate tools and machinery. The total flow requirement is typically calculated by summing the demands of all connected devices, taking into account their usage patterns and peak load conditions.
- Air Quality and purity: Required air quality varies by industry.
– ISO 8573-1 Class 1 is generally needed for pharmaceutical and food applications.
– Class 4 to 6 is typically sufficient for general manufacturing.
Filtration and drying systems must be selected accordingly to reach the desired dew point and remove oil, dust, and moisture from the air stream. Air Receiver sizing: An air receiver tank helps maintain system pressure and absorb fluctuations in demand. A common guideline is 3 to 5 gallons of tank capacity per CFM of compressor output. Proper tank sizing contributes to improved compressor efficiency and prolongs equipment lifespan.
- Altitude and ambient temperature: Compressor efficiency can be affected by environmental conditions. At higher altitudes, reduced air density results in lower compressor output. Elevated ambient temperatures may also impact performance and cooling efficiency. In such cases, the system may need to be adjusted or upscaled to maintain optimal operation.
- Horsepower (kW): The compressor’s power rating should align with the required pressure and flow rate. Higher horsepower generally translates into higher air output, although it also increases energy use. With Presscon’s PEC Controller, compressors of varying capacities (5kW, 25kW, or 100kW) can be managed intelligently to respond to actual demand levels.
- Pressure drop: Every system component introduces a degree of pressure loss. Keeping the total pressure drop below 0.5 bar helps maintain efficient performance. Filter monitoring and timely replacements, combined with a well-designed piping layout and appropriate pipe sizing, can help minimize pressure loss and reduce energy waste.
Optimal size is the most energy efficient
With Presscon’s expertise and the PEC Controller, we help you size your compressed air system precisely, based on real demand, future scalability, and your specific industry requirements. This results in:
- Lower energy costs
- Better system uptime
- Long-term reliability
Contact us for expert advice or a tailored consultation.
How does the compressed air system solution work in practice?
In a compressed air network or compressor park, for example, there are compressors of 2kW, 5kW, 25kW and 100kW. Suppose the demand for compressed air is so high that the three compressors with the least power cannot supply the demanded supply. A pressure-controlled system, at that moment switches on all four compressors in the park. This while the 100kW compressor alone is also capable of delivering the required power. The PEC Controller we developed controls the compressors on the basis of flow. In this situation, it switches on only the 100kW compressor from the beginning. For you as a business owner, this is the most energy-efficient choice that meets the compressed air demand.
The main advantage of flow control is the speed at which the system takes action to allow the compressor fleet to respond in a calm manner. This results in optimal energy consumption.
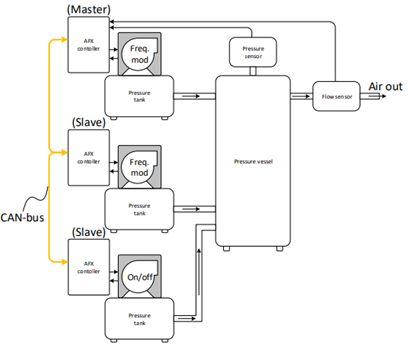
The compressed air system solution of Presscon: PEC Controller
In a compressed air network or compressor park, for example, there are compressors of 2kW, 5kW, 25kW and 100kW. Suppose the demand for compressed air is so high that the three compressors with the least power cannot supply the demanded supply. A pressure-controlled system, at that moment switches on all four compressors in the park. This while the 100kW compressor alone is also capable of delivering the required power. The PEC Controller we developed controls the compressors on the basis of flow. In this situation, it switches on only the 100kW compressor from the beginning. For you as a business owner, this is the most energy-efficient choice that meets the compressed air demand.
The main advantage of flow control is the speed at which the system takes action to allow the compressor fleet to respond in a calm manner. This results in optimal energy consumption.
We invented our own compressor control system: the PEC Controller. Our PEC Controller is a patented control module that optimizes compressor performance by managing one or more units based on real-time demand. As a result, the PEC Controller knows the status of the compressor and can control it in a targeted manner.
- Works with variable speed, rotary screw, and oil-free compressors.
- Adjusts output based on flow rate instead of pressure alone.
- Centralized control via touchscreen or Presscon Studio (TCP/IP).
- Supports remote locations with CAN bus or UDP communication.
- Monitors running hours, power consumption, and avoids resonant frequencies.
The PEC Controller can be used for virtually any type of compressor. Both for frequency-controlled compressors that switch on and off at a fixed power, as well as for variable frequency-controlled types. It is also possible to control compressors with multiple speed steps.
Benefits of the PEC Controller
- Energy savings through smart flow control
- Controls compressors centrally
- Compatible with many compressor brands
- Prevents unnecessary power consumption
- Real-time monitoring via touchscreen or Presscon Studio
Interested in reducing energy costs? Get in touch for a free consult.
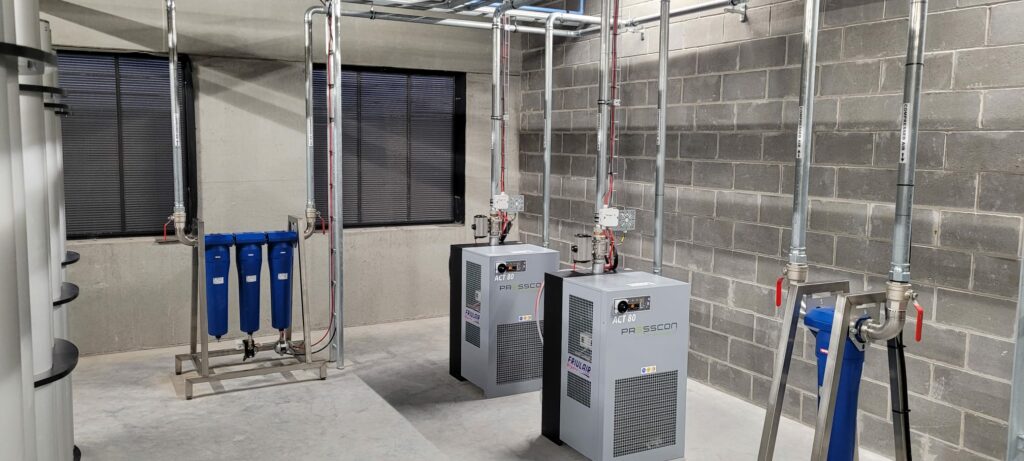
OUR NITROGEN GENERATORS
PRESSCON
- Monitor and control air pressure
- Keeps the pressure constant
- Efficient nitrogen cap
- Measure water levels
- ELC - SLC buffer tank measurement
- PLUG & PLAY installation
- Monitor and control air pressure
- Keeps the pressure constant
- Efficient nitrogen cap
- Measure water levels
- Adjustable to desired blow-off pressure
- Modular design
- Low energy consumption
- Long lifespan
- Multifunctional use
- Entirely organic
- Leaves no residue on the product
- On-site nitrogen production and thus not location
- Treatment in bulk possible
Ready to optimize your compressed air system?
Whether you use rotary screw air compressors or other industrial air compressors, choosing the right air compressor system ensures long-term performance and operational efficiency. With over 25 years of experience in the compressed air industry, Presscon offers smart, future-proof solutions for every situation. Our patented PEC Controller ensures optimal performance by intelligently managing air compressors of any size or type.
Whether you need to improve an existing air compression setup or design a new, energy-efficient system from the ground up, we’re here to help.
- Smart control of rotary screw compressors and oil-free compressors
- Efficient energy use through advanced air treatment solutions
- Reliable performance of every compressed air system component
- Long-term savings through reduced energy waste and better uptime
Check out other
Presscon products
- Filtering with very powerful magnets
- Visualize contamination with pressure gauges
- Automatic alarms and pressure switching
- Easy to connect to pump systems
- Multiple partial flow filters in one system
- Automatic alarms and pressure switching
- Easy to connect to pump systems
- Visualize contamination with pressure gauges
- +25 years of experience
- Own innovation and production department
- Custom
- Various connection options
- Sustainable and energy-efficient solutions
- +25 years of experience in compressed air
- Own innovation and production department
- Custom
- Sustainable and energy-efficient solutions