Compressed air installation
Grip on compressed air consumption
A compressed air system is an indispensable link in many production processes. Compressed air is a widely used, safe, but also expensive energy user. A small reduction in pressure therefore quickly provides significant financial benefits. We invented our own compressor control system: the PEC Controller. A patented control module to get a better grip on the operation of a compressor fleet and thus energy consumption.
The PEC Controller is a control system for controlling one or more compressors in a compressor fleet. It is a control module that we place in a compressor and have it communicate with the machine via digital and analog signals. As a result, the PEC Controller knows the status of the compressor and can control it in a targeted manner.
Need advice for your business or industry?
Compressed air solutions from Presscon
Presscon specializes in designing, building and maintaining nitrogen expansion systems, fire prevention systems and innovative solutions using compressed air and nitrogen and providing expert advice in that field. Compressed air generation has many different applications. Below are some of our products from a wide range of products:
- Connectable to many compressor types
- Ensures constant pressing pressure and flow rate
- Pairs compressors in separate rooms
- Efficient control of compressor fleet
- +25 years of experience in compressed air
- Own innovation and production department
- Custom
- Sustainable and energy-efficient solutions
Operation in park of compressors
The PEC Controller is primarily designed to be used in a fleet of several new compressors. Each compressor in the compressed air system is an essential component and has its own controller that communicate with each other via a CAN bus signal. As a result, the controllers know their status from each other and the control collectively determines which compressor turns on or off. We set one of the compressor controllers in the compressor park as the master controller. From there, the master coordinates the start and stop commands for all the individual “slave” controllers. This ensures efficiency, energy efficiency and longevity.
Designed from an energy conservation standpoint
We designed the control process of our compressor control system with efficient use of energy in mind. Our smart control module therefore aims to control each compressor in the park in such a way that it uses as little energy as possible while still delivering the desired flow (flow rate) and compressed air pressure. In other words, the PEC Controller ensures that the flow produced is equal to the flow demanded so that the pressure remains the same. In this process, the PEC Controller engages the most energy-efficient compressor. This makes our system unique compared to control systems that only look at compressed air pressure.
Works with any type of compressor
The PEC Controller can be used for virtually any type of compressor. Both for frequency-controlled compressors that switch on and off at a fixed power, as well as for variable frequency-controlled types. It is also possible to control compressors with multiple speed steps. Our compressor control system takes into account such things as after run time, power consumption at zero load, prohibited resonant frequencies, running hours and multiple factors that affect energy consumption.

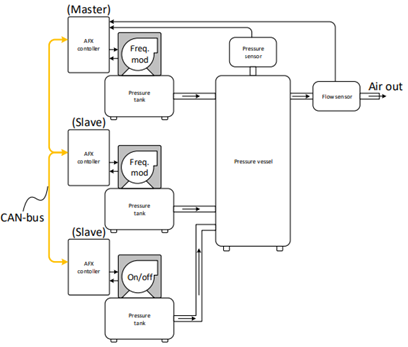
Central control of the new compressed air system
Each oil-free compressor in the new compressed air system has its own controller, so that all compressors in the compressed air system are controlled centrally. Even if they are in different locations. The compressor controllers communicate via a CAN bus network or via UDP over LAN, making it possible to control them from a central point. With a clear touch screen display, each machine can also be accessed and set individually. The PEC can be accessed via TCP/IP using our Windows application: Presscon Studio. With this software, as with the touchscreen display, it is possible to read out the status of the machines, view alarm messages and change settings of control modules.
In practice
In a compressed air network or compressor park, for example, there are compressors of 2kW, 5kW, 25kW and 100kW. Suppose the demand for compressed air is so high that the three compressors with the least power cannot supply the required demand. A pressure-controlled system, at that moment switches on all four compressors in the park. This while the 100kW compressor alone is also able to deliver the required power. The PEC Controller we developed controls the compressors on the basis of flow. In this situation, it switches on only the 100kW compressor from the beginning. For you as a business owner, the most energy-efficient choice that meets the demand for compressed air.
The main advantage of flow control is the speed with which the system takes action to make the compressor fleet respond in a calm manner. This results in optimal energy consumption.
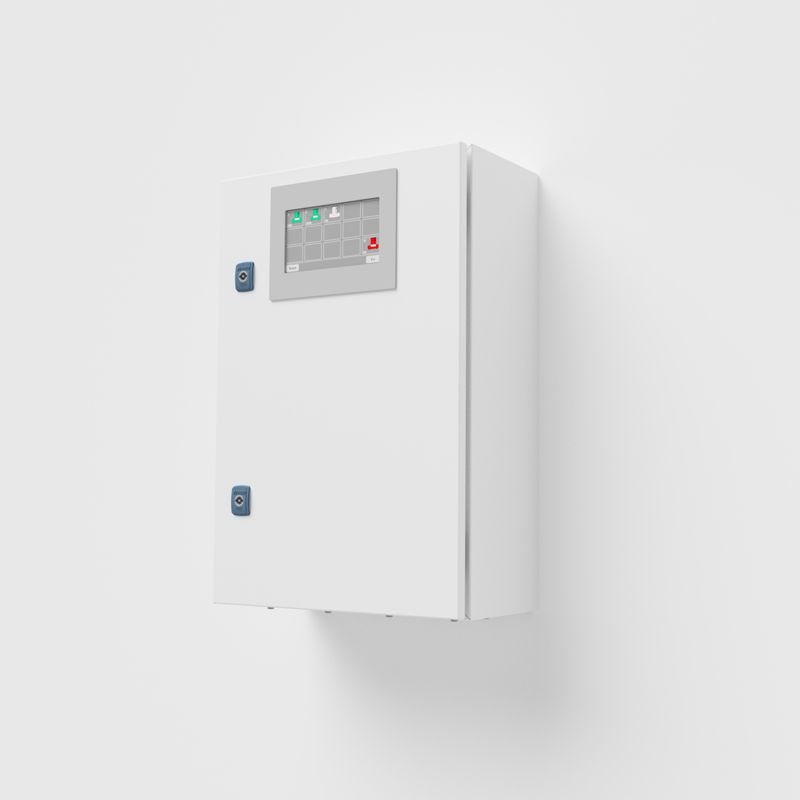
Schematic representation of a compressor fleet
The setup below is an example of a compressor fleet with three compressors controlled by the PEC Controller. Visible is how the elements are connected to each other and how they communicate. With the PEC Controller, it is possible to control up to fifteen machines.
The premise of the PEC Controller is to provide constant compressed air pressure and flow as efficiently as possible. Here, the compressor control system looks at the decrease in flow rate, simultaneously takes into account the desired compressed air pressure and combines that with the knowledge of when which compressor is most energy efficient.
The main advantage of a flow controller is the speed with which it takes action to make the compressor fleet respond in a calm manner. This results in optimal energy consumption. This is because a direct measurement in variation of flow (flow) is faster, than a measurement in variation of air pressure.
The PEC Controller
- Provides greater control over compressor fleet operation and energy consumption.
- Provides energy savings averaging 15% by switching on the most efficient compressor at the right time.
- Can be used for any type of compressor.
- Can control, location independent, up to 15 compressors within the same compressor fleet.
- Can control compressors of different powers in a compressor fleet.
Discover the power of compression
With a compressor, air is compressed to a certain pressure. When air is compressed, the molecules move faster and the temperature rises. This phenomenon is called compression heat. Compression literally forces the dry air into a smaller space, bringing the molecules closer together.
The energy released is equal to the energy needed to squeeze the air into the smaller space. In other words, the energy is stored for later use. Consider, for example, a balloon that “flies away” as soon as you puncture it.
Using compressed air efficiently
“Is there any compressed air available?” is one of the first questions we ask as Presscon at an introduction. By thinking this through at an early stage, in many cases we provide a more efficient compressed air solution. For example, we may be able to supply one large, frequency-controlled compressor, rather than a number of smaller compressors. The result is a more professional and reliable process that is easier to maintain, less complex and more economical.
A complete compressed air system put together based on expert advice ensures compressed air for the proper operation of your production process. This often requires additional equipment, in the form of professional installation of compressed air piping and equipment, such as: pressure vessels and filters and adsorption or freeze dryers, to remove oil and water from the compressed air. Piping is available in various diameters.